The Plastic Workhorse: Unveiling the Power and Versatility of PP Sheet
- Priyanshu SEO
- May 18, 2024
- 5 min read
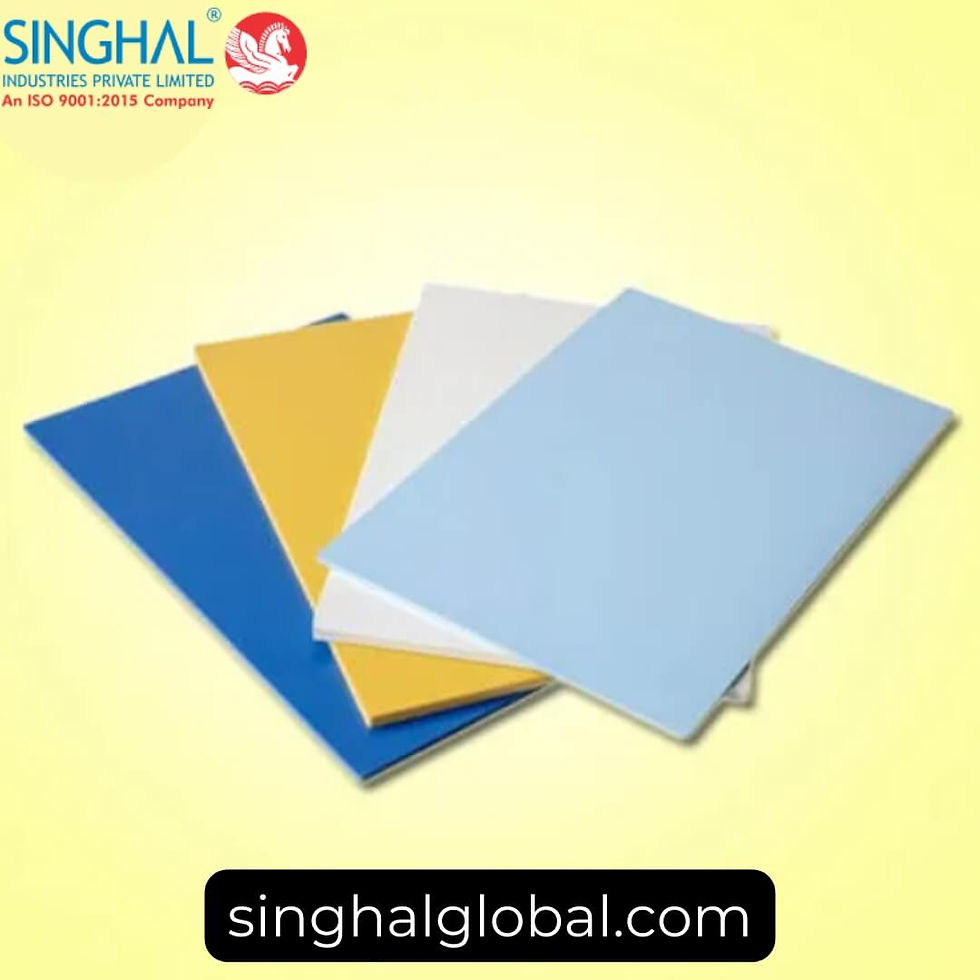
Polypropylene (PP) sheets are a versatile and widely used plastic material known for their excellent properties and wide range of applications. These sheets are used in various industries, including packaging, automotive, construction, and healthcare. This comprehensive guide explores the characteristics, production process, applications, and benefits of PP sheets.
What are PP Sheets?
Definition and Composition
PP sheets are flat, rigid panels made from polypropylene, a thermoplastic polymer. Polypropylene is a type of plastic known for its durability, chemical resistance, and versatility. PP sheets Manufacturers are available in various thicknesses, colors, and surface finishes, making them suitable for numerous applications.
Properties of PP Sheets
PP sheets exhibit several key properties:
High Impact Resistance: PP sheets price are resistant to impact and can withstand rough handling and stress without breaking or cracking.
Chemical Resistance: These sheets are resistant to many chemicals, acids, and alkalis, making them ideal for use in harsh environments.
Lightweight: Polypropylene is a lightweight material, making PP sheets easy to handle and transport.
Moisture Resistance: PP sheets do not absorb moisture, ensuring they remain stable and maintain their properties in wet conditions.
Thermal Resistance: They can withstand high temperatures and are often used in applications requiring heat resistance.
Recyclability: Polypropylene is recyclable, and PP sheets can be reprocessed and reused, contributing to environmental sustainability.
Production Process of PP Sheets
Extrusion
The production of PP sheets begins with the extrusion process. Polypropylene resin is melted and forced through a flat die to form a continuous sheet. The thickness of the sheet is controlled by the die opening and the speed of the extrusion process.
Cooling and Calibration
The extruded PP sheet is then passed through a series of cooling rolls to solidify the material. After cooling, the sheet goes through calibration rollers to ensure it has a uniform thickness and a smooth surface finish.
Cutting and Finishing
Once the sheet is calibrated, it is cut to the desired size using precision cutting equipment. Additional finishing processes, such as surface texturing or printing, may be applied to meet specific requirements.
Quality Control
Each PP sheet undergoes rigorous quality control checks to ensure it meets industry standards. These checks include testing for thickness uniformity, surface quality, and mechanical properties.
Applications of PP Sheets
Packaging
PP sheets suppliers are extensively used in the packaging industry for:
Food Packaging: Due to their chemical resistance and moisture barrier properties, PP sheets are ideal for food packaging applications.
Blister Packs: They are used to create blister packs for pharmaceuticals and consumer goods, providing a durable and protective packaging solution.
Stationery and Folders: PP sheets are used to manufacture stationery products such as folders, binders, and covers.
Automotive
In the automotive sector, PP sheets are used for:
Interior Components: PP sheets are used to make interior components such as door panels, dashboards, and trim parts due to their lightweight and durable nature.
Battery Covers: Their chemical resistance makes PP sheets suitable for manufacturing battery covers and other under-the-hood components.
Construction
In construction, PP sheets serve various purposes, including:
Formwork: PP sheets are used as formwork for concrete casting due to their strength and ease of handling.
Insulation: They are used as thermal and acoustic insulation in buildings, providing energy efficiency and noise reduction.
Healthcare
PP sheets are widely used in the healthcare industry for:
Medical Trays and Containers: Their chemical resistance and easy sterilization make them ideal for medical trays, containers, and other equipment.
Protective Barriers: PP sheets are used to create protective barriers and partitions in medical facilities.
Signage and Displays
PP sheets are also used for creating signage and display materials, including:
Advertising Boards: Their durability and printability make them suitable for outdoor advertising boards and signs.
Point of Sale Displays: PP sheets are used to create attractive and sturdy point of sale displays for retail environments.
Advantages of PP Sheets
Durability and Strength
One of the primary advantages of PP sheets is their durability and strength. They can withstand impact, chemical exposure, and harsh environmental conditions, making them suitable for demanding applications.
Versatility
PP sheets are versatile and can be used in a wide range of applications across different industries. Their adaptability in terms of thickness, color, and surface finish allows for customized solutions.
Lightweight and Easy to Handle
PP sheets are lightweight, making them easy to handle, transport, and install. This property is particularly advantageous in construction and automotive applications where weight reduction is essential.
Chemical and Moisture Resistance
The chemical and moisture resistance of PP sheets ensures their longevity and performance in challenging environments. They do not corrode or degrade when exposed to chemicals or moisture, making them ideal for packaging and healthcare applications.
Cost-Effectiveness
PP sheets offer a cost-effective solution compared to other materials with similar properties. Their recyclability and durability reduce the need for frequent replacements, resulting in cost savings over time.
Environmental Sustainability
Polypropylene is a recyclable material, and efforts are being made to enhance the recycling processes for PP sheets. Recycling helps reduce the environmental impact and promotes sustainability in industries that rely on these sheets.
Environmental Considerations
Recycling and Reusability
Polypropylene is a recyclable material, and PP sheets can be reprocessed and reused. This recyclability contributes to reducing waste and promoting a circular economy.
Biodegradable Alternatives
Research is ongoing to develop biodegradable alternatives to traditional PP sheets. These alternatives aim to provide the same benefits while reducing the environmental footprint, offering a more sustainable option for the future.
Conclusion
PP sheets are a versatile and essential material used across various industries due to their excellent properties, including durability, chemical resistance, and recyclability. From packaging and automotive to construction and healthcare, these sheets provide practical solutions for numerous applications. Understanding the properties, production process, applications, and advantages of PP sheets enables businesses to make informed decisions and leverage the benefits of this remarkable material.
Frequently Asked Questions about PP Sheets:
1. What are PP Sheets?
PP Sheets, or polypropylene sheets, are thermoplastic polymer sheets made from polypropylene (PP) resin. They are known for their excellent chemical resistance, durability, and versatility. These sheets are used in a variety of industries for applications such as packaging, automotive, construction, and printing.
2. What are the common uses of PP Sheets?
Common uses of PP Sheets include:
Packaging: Used for creating boxes, containers, and other packaging materials due to their lightweight and durable properties.
Automotive: Employed in manufacturing automotive parts like battery casings, interior trim, and protective barriers.
Construction: Utilized in building materials such as cladding, roofing, and protective barriers.
Printing and Signage: Used for producing signs, displays, and print advertising materials due to their smooth surface and printability.
Stationery: Applied in making files, folders, and other office supplies.
Medical: Used for making disposable medical products and protective barriers.
3. What are the advantages of using PP Sheets?
The advantages of using PP Sheets include:
Chemical Resistance: Highly resistant to a wide range of chemicals, making them suitable for various industrial applications.
Durability: Strong and durable, capable of withstanding physical stress and impact.
Lightweight: Significantly lighter than many other plastic materials, making them easy to handle and transport.
Thermal Resistance: Can withstand high temperatures without deforming, making them suitable for hot-fill applications.
Non-Toxic and Safe: Safe for use in food packaging and medical applications.
Recyclable: Environmentally friendly as they can be recycled and reused.
4. How are PP Sheets manufactured?
The manufacturing process of PP Sheets involves:
Extrusion: Polypropylene resin is melted and extruded through a flat die to form a continuous sheet.
Cooling: The extruded sheet is passed through cooling rolls to solidify and achieve the desired thickness.
Cutting: The cooled sheet is cut into specific sizes as per the requirements.
Finishing: Additional treatments such as corona treatment may be applied to enhance surface properties for printing or bonding.
5. Can PP Sheets be customized?
Yes, PP Sheets can be customized to meet specific requirements. Customization options include:
Size and Thickness: Available in a range of sizes and thicknesses to suit different applications.
Colors: Can be produced in various colors for aesthetic or functional purposes.
Surface Finish: Available in different surface finishes such as smooth, matte, or textured.
Additives: Can include additives for UV resistance, flame retardancy, or enhanced strength.
Printing: Printable surfaces for branding, instructions, or decorative purposes.
Comments